Kneu-crete aims to interrogate and establish a material dialogue between CNC-knitted inflatable formworks and concrete. Attempting to redefine the role of concrete within formwork, where it acts as an active contributor rather than a passive one, becoming a driving agent for form-finding and slumping control within the casting process as opposed to merely taking shape from a rigid mold. The research investigated computational and physical methods simultaneously to generate and understand doubly curved, flat, or ruled surfaces. The main challenge of applying flexible fabric formwork into real construction practices is control and translation; translating the desired digital geometry into a relaxed flat geometry and then into a tensioned geometry. This integration of computational design and physical experiments aims to develop a viable workflow which allows data to transmit among digital and physical models along with potential design solutions.Initial studies described in this project use digital simulations and physical experiments to understand and anticipate the material dialogue between the kneu-crete system, creating a taxonomy to index procedural slumping within CNC-knitted inflatable formwork through material programming at a micro-level. The computational method is used to develop the textile component of the system, both in design and fabrication. In the digital simulation, a design workflow was developed to separate the computational task into two parts, global and local deformation, to make the simulation process more efficient. The acquired information from the two simulated resolutions (micro/macro deformations) provide numerical data detailing the type of action to be executed by the CNC-Knitting machine such as stitch structure, stitch type, stitch length, and overall knit dimensions.The system’s feasibility is explained and studied through the design and analysis of nine distinct CNC-knitted textiles and glass fiber reinforced concrete panels, where each panel explores the capacity of different stitch structures and integration of stitch lengths at a cellular level to influence the overall form and topology of the surface. This series of prototypes which aim to depict the potentials of the hybrid system places materiality as a priori agent and generator of complex forms and control. By measuring the simulation outcome with scan data from a physical experiment, the data emerged into a set of knowledge to bridge the gap between digital and analog. This process helps in the creation of a feedback loop to better understand and digitally foresee material behaviour under different specified conditions such as types of yarn, stitch structure, gravity, and weights.The other facet of this research regarding development involved the application of physical methods. Utilizing weights, pre-stress was applied to the textile component in addition to the weight of the concrete to utilize the integrated tensile behavior of the elastic yarns to fix the three-dimensional formwork. The variation in the three-dimensional outcome was essentially a result of the knit structure and the interconnection of differentiated material properties in addition to external uniform weights across the region
This programmable formwork challenges the presumed configuration of concrete casting. The architectural qualities emerge from the fine grains produced technologically by the CNC Knitting machine in contrast with the material nature of concrete. The scale and nature of the surface offer a significant opportunity for redevelopment to harmonize the material process with digital and robotic workflow. The ability to respond to variables from materials and environment, gravity, weight, tensile strength, and the control of the symmetrical and asymmetrical slump build the foundation of digital materials discourse.
Project Team: Shan Chun Wen (Project Lead), Maryam AlJomairi (Project Lead), Misri Patel
CNC Knitting Collaborator: Tracey Weisman
Instructor : Glenn Wilcox
Spring 2019 - University of Michigan
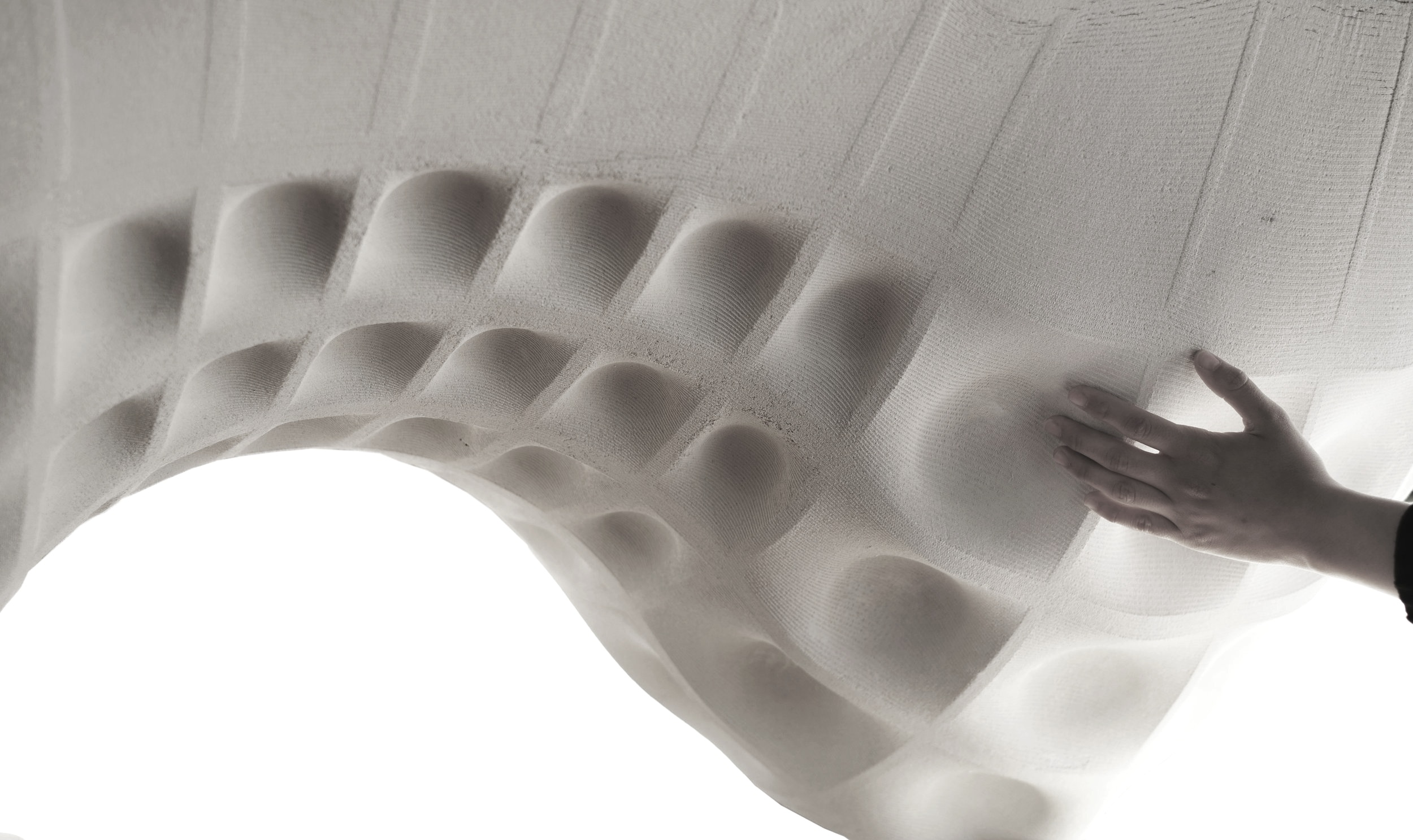
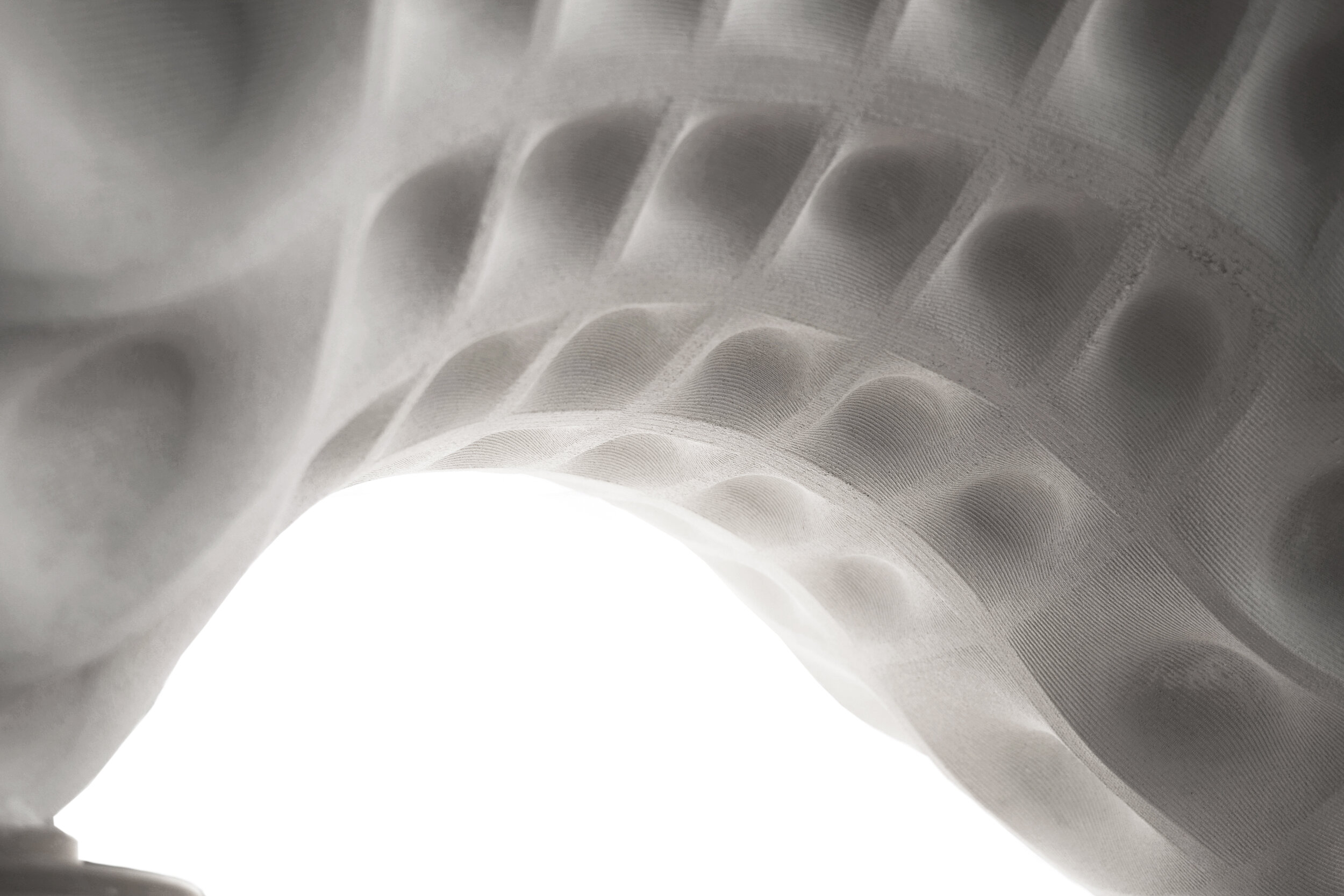
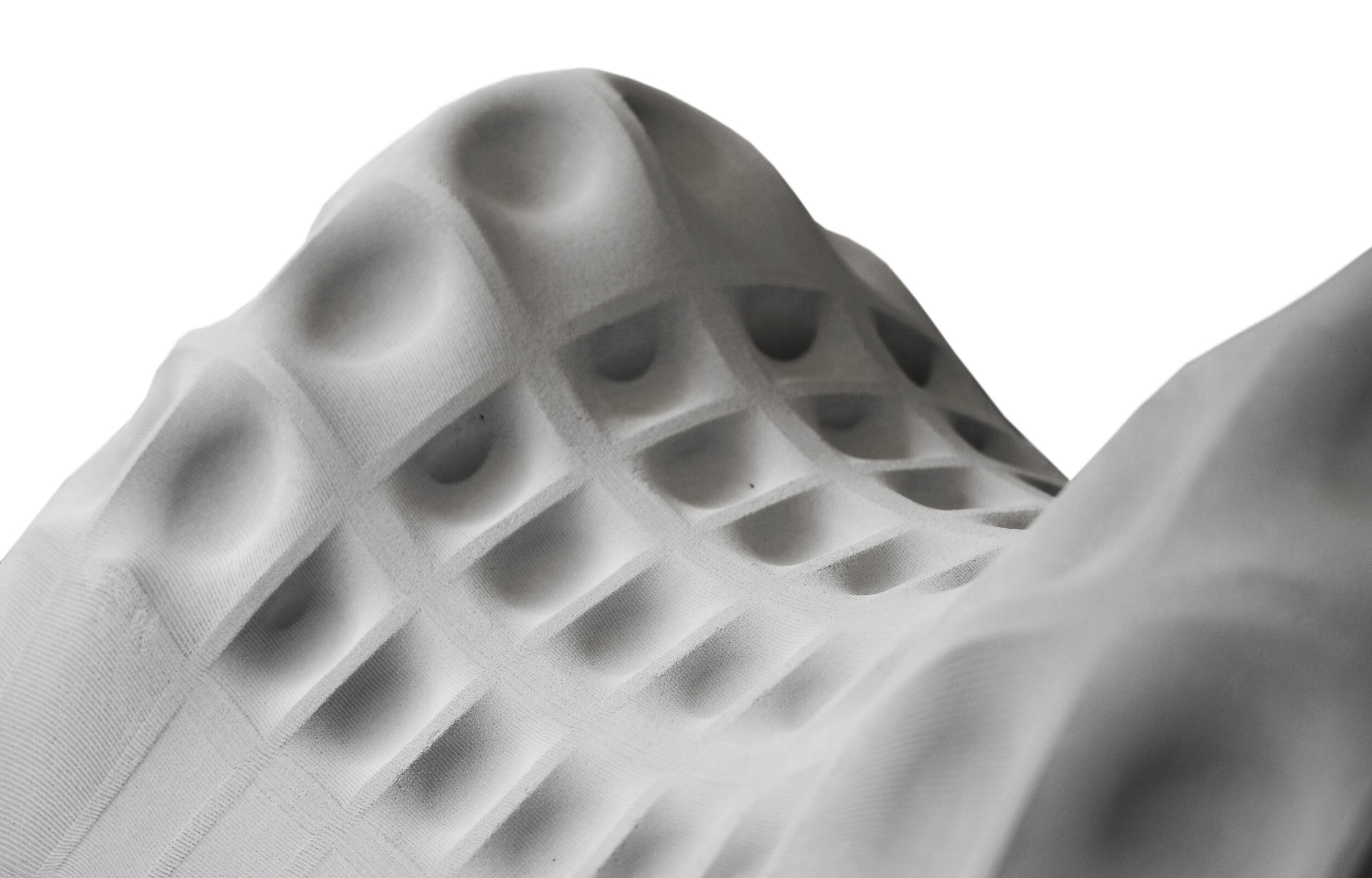
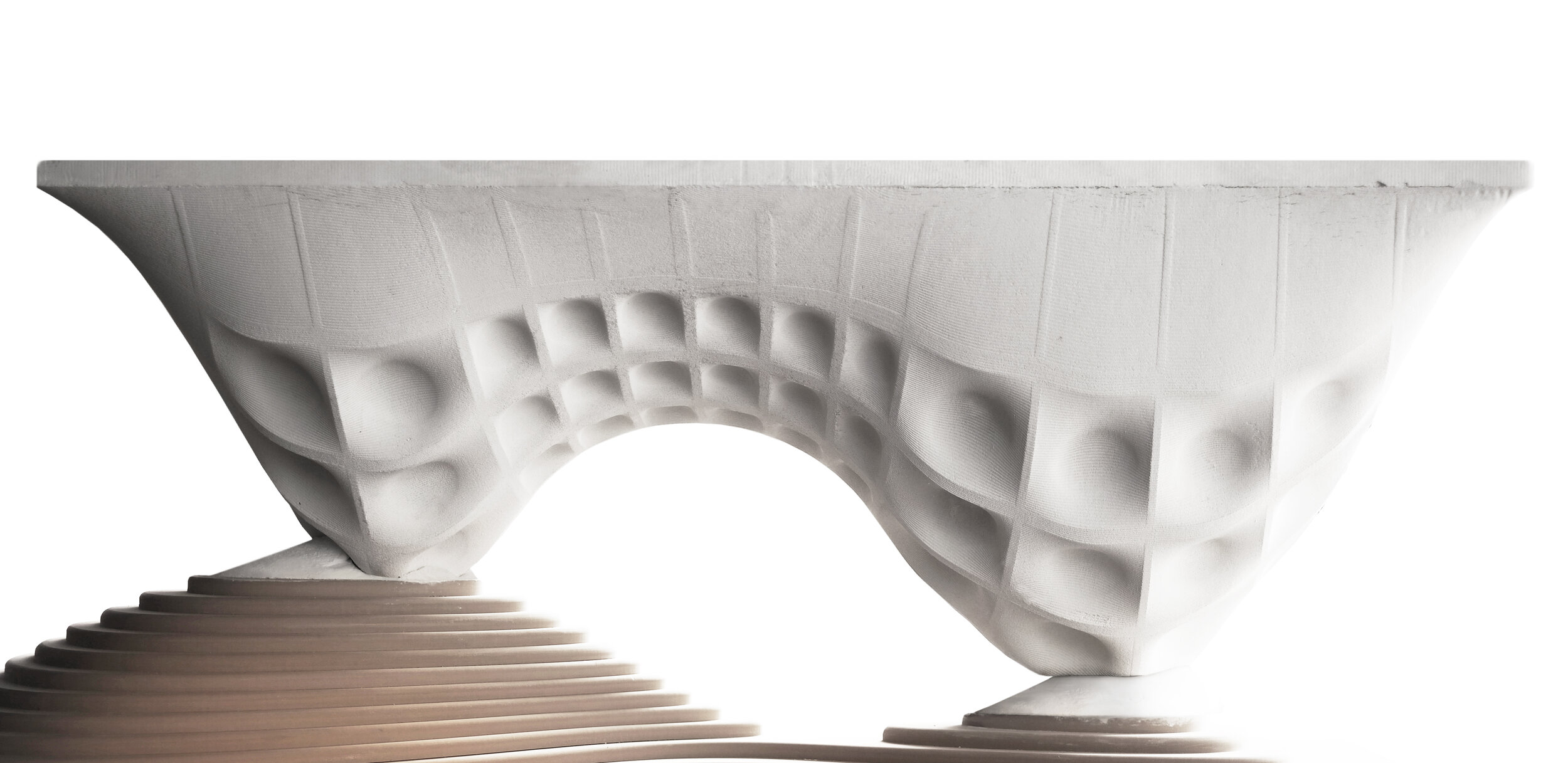
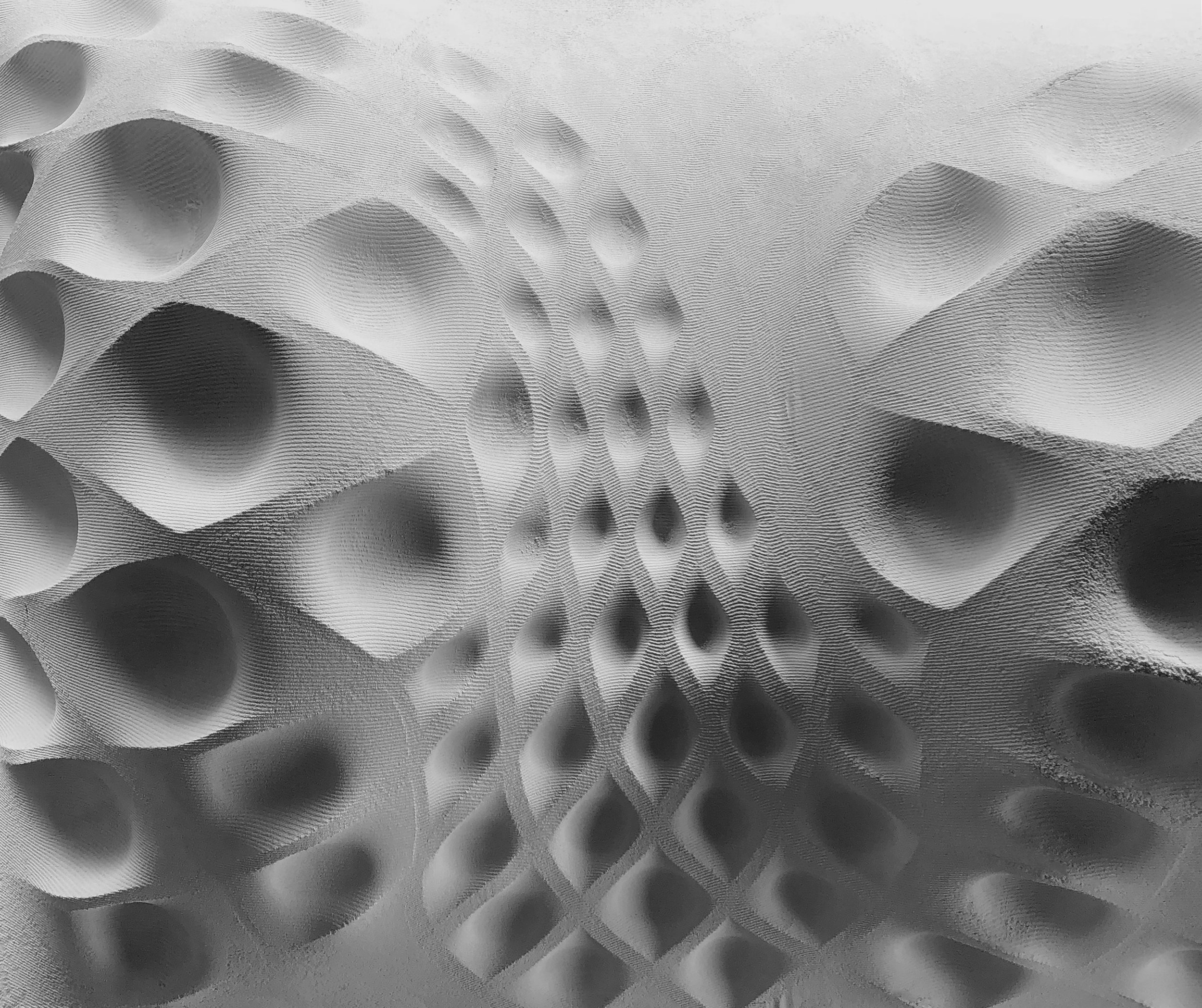
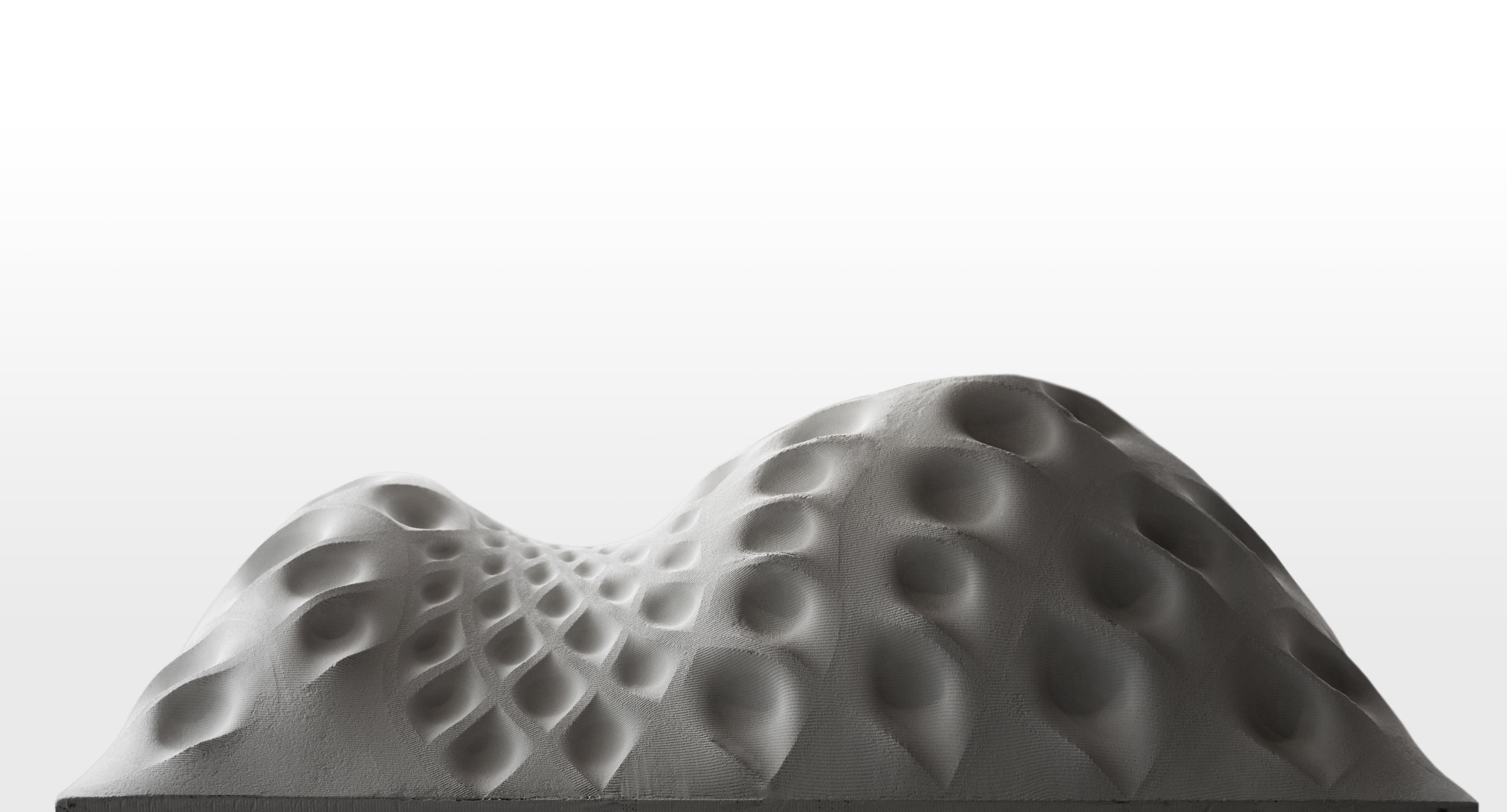
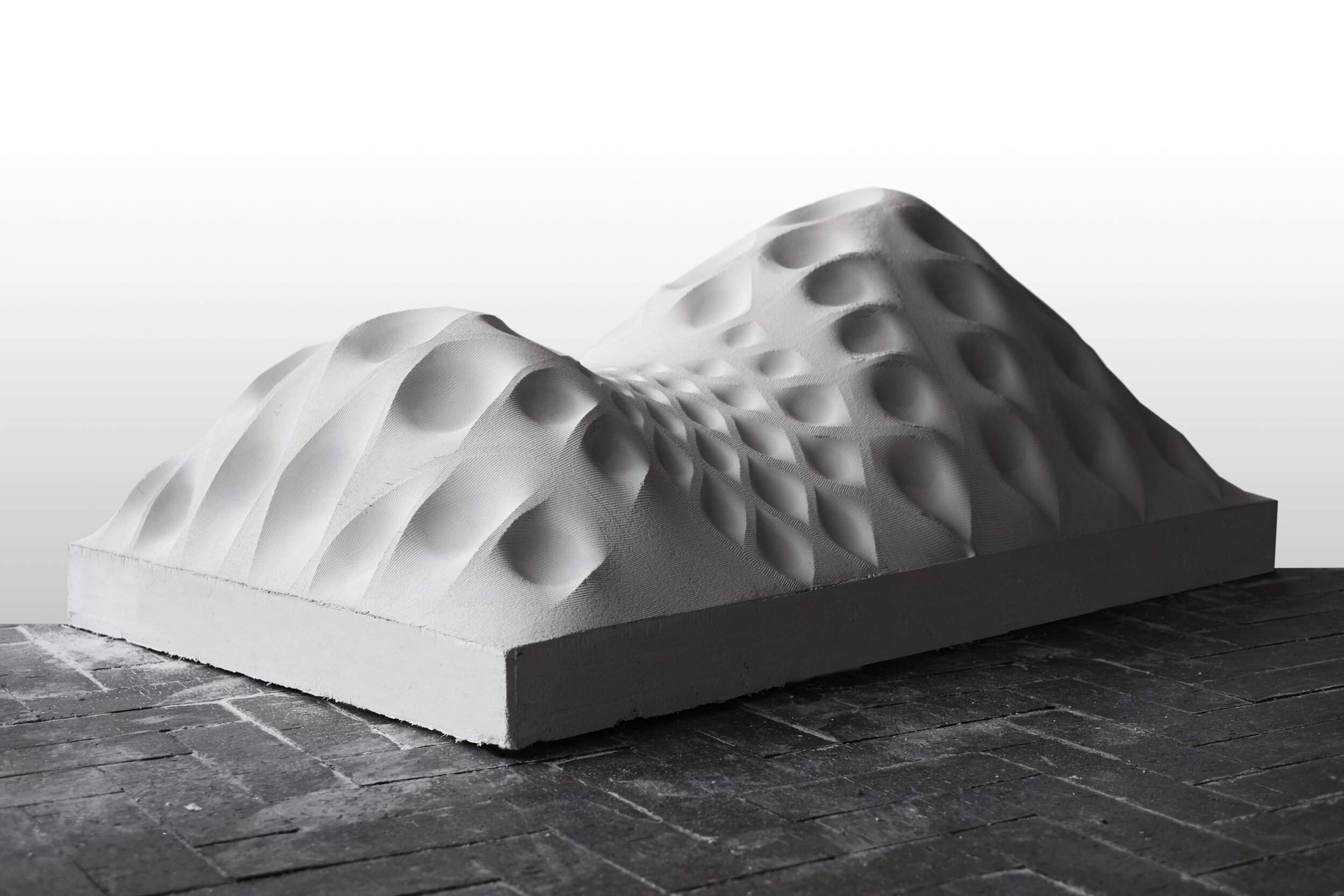